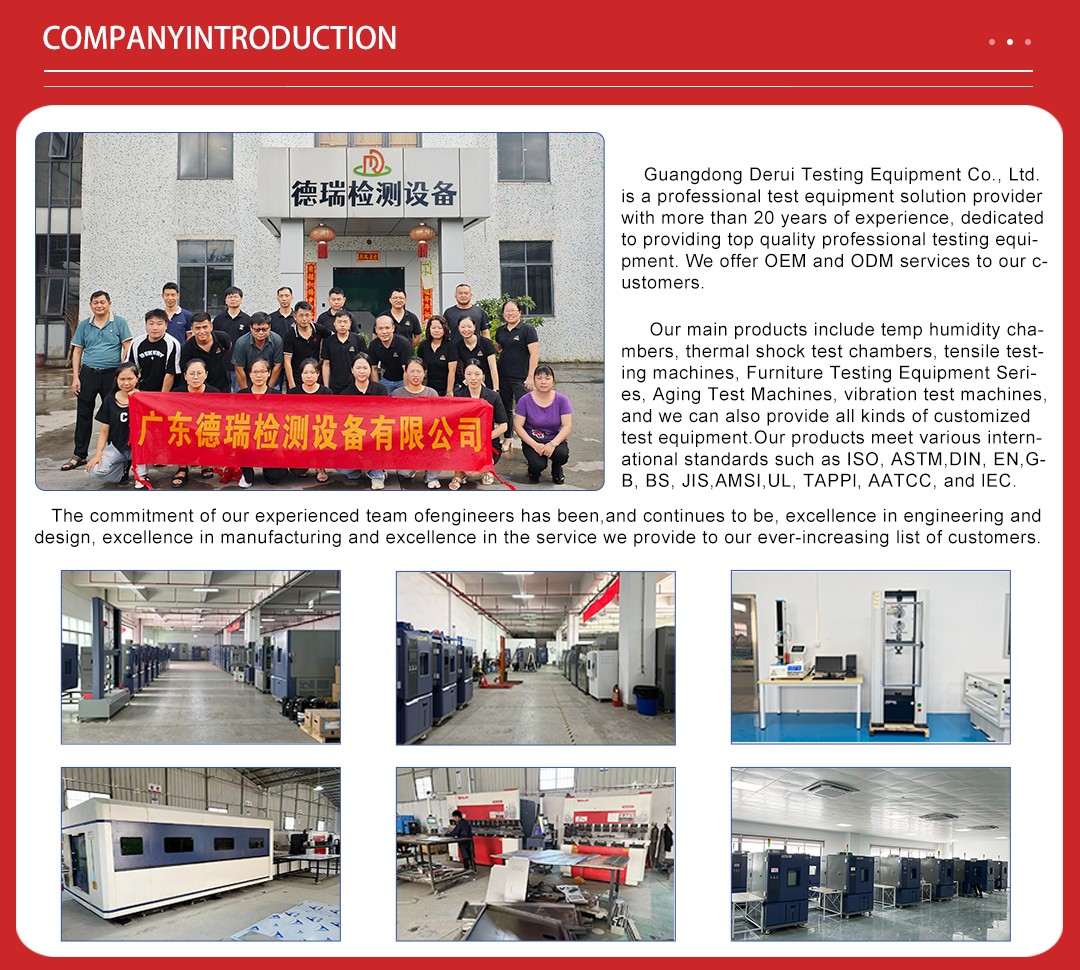
The Rapid Thermal Cycling Chamber is a highly specialized environmental testing solution meticulously designed to meet the demanding requirements of the aerospace industry. This advanced equipment is instrumental in simulating the extreme and rapid temperature fluctuations that spacecraft components, subsystems, and materials encounter during various phases of space missions.

In the aerospace industry, the Rapid Thermal Cycling Chamber serves a multifaceted role:
1. Component Qualification: Validates the performance and reliability of individual components under extreme temperature conditions, ensuring they meet mission-critical requirements.
2. Subsystem Integration Testing: Assesses the combined performance of integrated subsystems under thermal stress, identifying potential points of failure and optimizing overall system design.
3. Material Characterization: Evaluates the thermal properties and behavior of materials used in spacecraft construction, ensuring their suitability for space applications.
4. Mission Simulation: Replicates the temperature extremes encountered during launch, orbital flight, and re-entry, providing a comprehensive understanding of spacecraft performance throughout the mission lifecycle.

1. Wide Temperature Range: Capable of achieving temperatures ranging from -196°C to 500°C, accommodating the extreme cold of deep space and the intense heat of atmospheric re-entry.
2. Exceptional Temperature Transition Rates: Provides rapid heating and cooling rates, exceeding 60°C per minute, to replicate dynamic temperature shifts encountered in space.
3. Precise Temperature Control: Equipped with advanced control systems, ensuring precise and uniform temperature distribution within ±1°C tolerance.
4. Customizable Test Profiles: Allows users to program complex temperature cycles with varying ramp rates, dwell times, and cycle repetitions, tailoring tests to specific mission profiles.
5. Data Acquisition and Monitoring: Integrated data acquisition systems continuously monitor and record temperature data, providing real-time insights and facilitating post-test analysis.
6. Safety and Reliability: Incorporates robust safety interlocks, alarms, and fail-safe mechanisms, ensuring operator safety and preventing equipment damage.
7. Versatile Testing Capabilities: Supports a wide range of test specimen sizes and configurations, from small components to large subsystems, accommodating diverse testing needs.

Model | DR-H204-100 | DR-H204-150 | DR-H204-225 |
Internal dimension | 400*500*500mm | 500*600*500mm | 600*750*500mm |
External dimension | 750*1536*1310mm | 750*1636*1410mm | 850*1786*1410mm |
Temperature(℃) | -20/-40/-70 | -20/-40/-70 | -20/-40/-70 |
Maximum Current(A) | 22,22,28 | 22,22,28 | 18,18,23 |
Voltage(V) | Single-phase220V | Single-phase220V | Three-phase380V |
Temp,range | 0℃;-20℃;-40℃;-70℃~+150℃ |
Test Method | Pneumatic Operated Door Switch(two/three-zone) |
Temp.Display Accuracy | 0.01℃ |
Temp.uniformity | ≤±2.0℃ |
Temp.deviation | ±0.5℃~±0.2℃(without load) |
Heating speed | 1℃/min~20℃/min,can be customized |
Cooling Speed | 1℃/min~20℃/min,can be customized |
Humid.range | 20%~98%RH |
Humid.resolution | 0.1% R.H. |
Humid.uniformity | ±3%RH(without load) |
Internal chamber material | Stainless steel 304 |
External chamber material | Stainless steel/paint spray |

Working Principle
The Rapid Thermal Cycling Chamber operates on the principle of rapid and uniform temperature changes, achieved through a sophisticated interplay of advanced heating and cooling systems. The working cycle typically comprises the following phases:
1. Initial Stabilization: Establishing a baseline temperature and allowing the test specimen to reach thermal equilibrium.
2. Rapid Heating: Quickly increasing the temperature to simulate heat-generating events such as atmospheric re-entry, solar radiation, or internal heat dissipation.
3. Temperature Hold: Maintaining a constant elevated temperature for a specified duration to assess the test specimen's steady-state thermal performance.
4. Rapid Cooling: Swiftly decreasing the temperature to replicate the extreme cold of space or high-altitude flight, evaluating the test specimen's response to thermal shock.
5. Final Stabilization: Returning the chamber to ambient temperature, allowing the test specimen to reach thermal equilibrium before removal.
Test Significance and Data Interpretation
The data obtained from Rapid Thermal Cycling Chamber tests provide critical insights into the performance and behavior of aerospace components under extreme temperature conditions. Through comprehensive analysis, engineers can:
1. Assess Thermal Endurance: Evaluate the test specimen's ability to withstand rapid temperature changes and prolonged exposure to extreme temperatures. 2. Identify Failure Modes: Detect potential points of failure, such as material degradation, structural fatigue, or component malfunction, under thermal stress.
3. Validate Design Margins: Verify that components and subsystems meet design margins and safety factors, ensuring their reliable operation within specified temperature limits.
4. Optimize Thermal Management: Refine thermal management strategies, such as passive or active cooling systems, to enhance the overall performance and efficiency of spacecraft.
5. Support Modeling and Simulation: Provide empirical data to validate and calibrate computational models, enabling more accurate prediction of spacecraft behavior under various thermal scenarios.
Main Components and Configurations
The Rapid Thermal Cycling Chamber consists of several key components that can be configured to meet specific testing requirements:
1. Insulated Test Chamber: A thermally isolated enclosure designed to minimize heat transfer with the external environment, ensuring precise temperature control. 2. Heating and Cooling Systems: High-performance heating elements and refrigeration units capable of rapid temperature changes and tight control.
3. Temperature Sensors and Probes: Precision sensors strategically placed within the chamber to monitor temperature distribution and provide real-time feedback to the control system.
4. Programmable Control Unit: An advanced control interface allowing users to program complex temperature cycles, set control parameters, and monitor test progress.
5. Data Acquisition and Monitoring Software: Integrated software solutions for real-time data visualization, recording, and post-test analysis.
6. Safety Systems: Comprehensive safety features, including interlocks, alarms, and emergency stop mechanisms, ensuring operator safety and equipment protection.
7. Vacuum and Humidity Control: Optional configurations for combining temperature cycling with vacuum or humidity control, replicating the complex environmental conditions encountered in space.
Operating Procedures and Best Practices
To ensure accurate and reliable test results, it is essential to follow established operating procedures and best practices when using the Rapid Thermal Cycling Chamber:
1. Test Planning: Carefully plan the test profile, considering the specific requirements of the component or subsystem under test, as well as the relevant mission scenario.
2. Specimen Preparation: Properly prepare the test specimen, ensuring it is clean, free of contaminants, and instrumented with any necessary sensors or data acquisition equipment.
3. Chamber Setup: Configure the chamber according to the test plan, setting temperature ranges, ramp rates, dwell times, and other control parameters.
4. Calibration: Regularly calibrate temperature sensors and other measurement devices to maintain accuracy and traceability.
5. Test Execution: Initiate the test cycle, continuously monitoring the chamber's performance and the test specimen's response through the control interface.
6. Data Collection: Record and store temperature data, as well as any other relevant measurements, for post-test analysis.
7. Safety Monitoring: Remain vigilant for any signs of equipment malfunction or safety concerns, prepared to intervene and abort the test if necessary.
8. Post-Test Inspection: Upon completion of the test cycle, carefully inspect the test specimen for any signs of damage, degradation, or other notable changes.
9. Data Analysis: Thoroughly analyze the collected data, drawing insights into the test specimen's performance and identifying areas for improvement or further investigation.
The Rapid Thermal Cycling Chamber is an indispensable tool in the aerospace industry, enabling engineers to subject spacecraft components, subsystems, and materials to the extreme temperature conditions encountered during space missions. By providing precise temperature control, rapid transition capabilities, and versatile testing configurations, the chamber facilitates comprehensive evaluation of thermal performance and endurance. Through rigorous testing and data analysis, the Rapid Thermal Cycling Chamber plays a vital role in ensuring the reliability, safety, and success of space missions, driving innovation and advancement in aerospace technology.
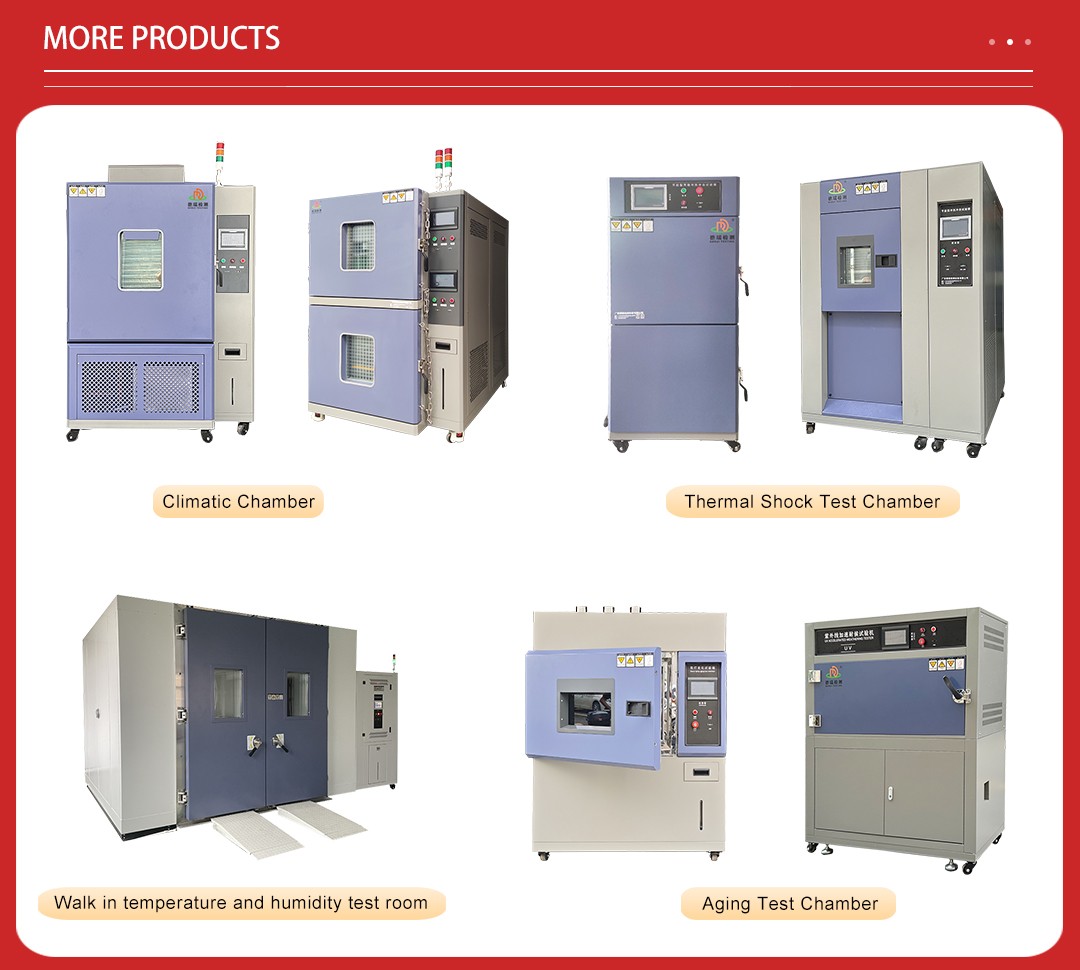
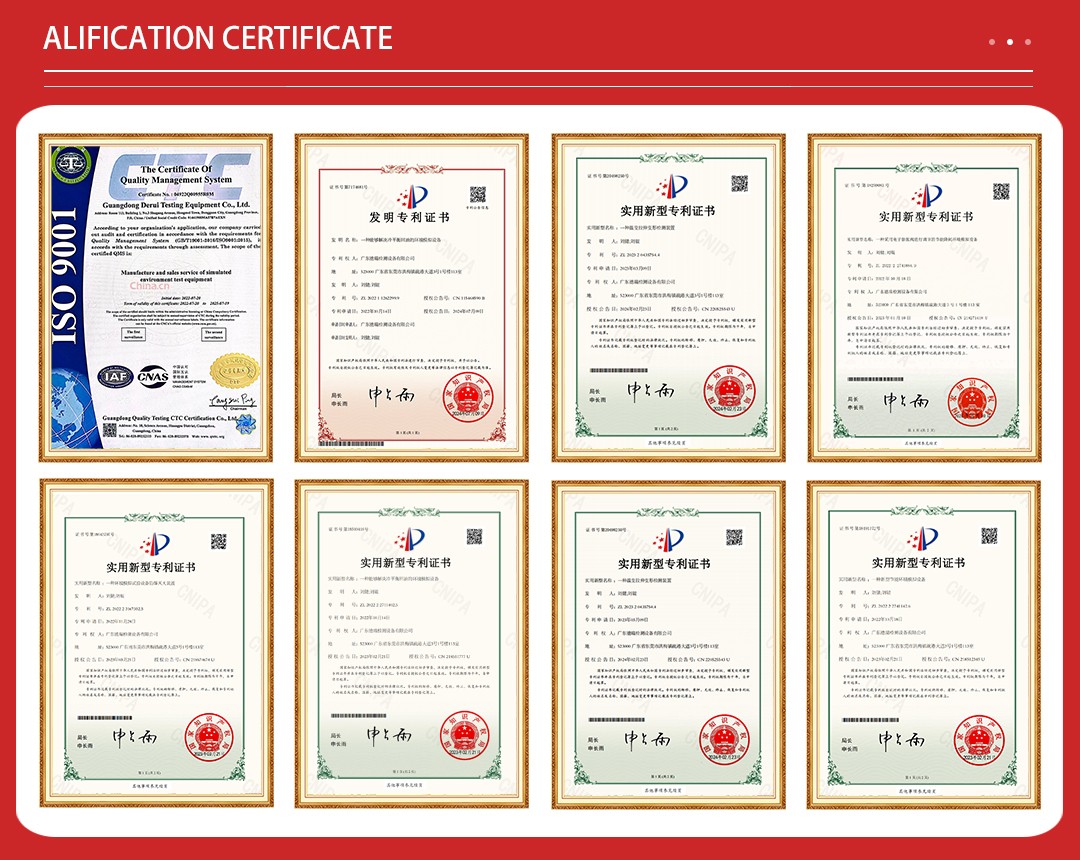