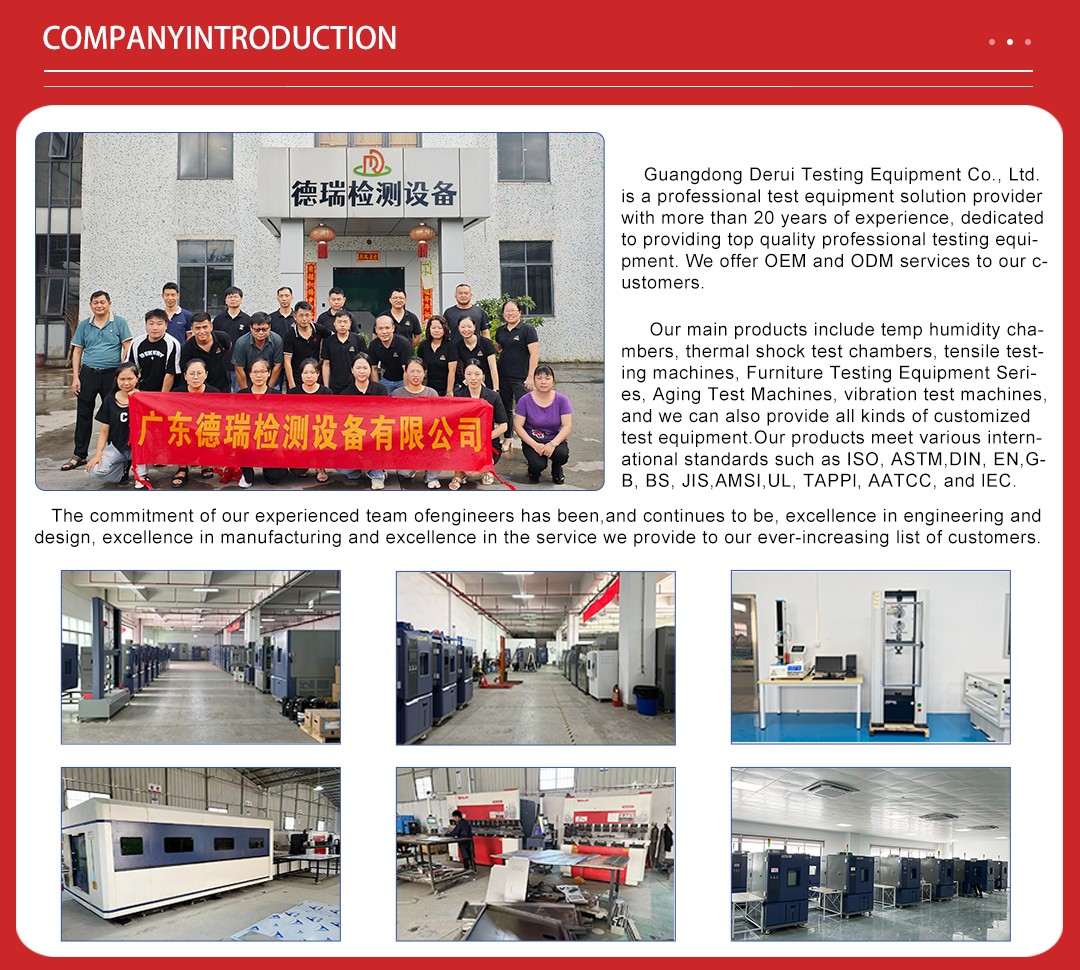
The Ultraviolet (UV) Aging Test Chamber is a specialized piece of equipment designed to simulate and accelerate the aging process of plastic materials under controlled UV light exposure. This device is crucial for assessing the durability, stability, and longevity of plastics when subjected to long-term sunlight or artificial UV radiation. By exposing samples to intense UV light, combined with temperature and humidity control, the chamber provides valuable insights into how materials will perform over time in real-world conditions.

- Polymer Degradation Studies: Evaluates the resistance of polymers to UV-induced degradation, helping manufacturers select the most durable materials for outdoor applications.
- Additive Performance Testing: Assesses the effectiveness of UV stabilizers, antioxidants, and other additives in enhancing the long-term stability of plastic formulations.
- Product Development: Accelerates the development cycle by quickly identifying potential issues with new materials or product designs, allowing for timely adjustments before mass production.
- Quality Assurance: Ensures that plastic products meet specified durability and performance standards, reducing the risk of premature failure in the field.
- Market Compliance: Helps manufacturers comply with international and industry-specific standards, facilitating market entry and customer confidence.

The operation of UV aging test chambers should adhere to relevant international and industry-specific standards, including:
- ISO 4892-2: Plastics – Methods of exposure to laboratory light sources – Part 2: Xenon-arc lamps
- ASTM G154: Standard Practice for Operating Fluorescent Light Apparatus for UV Exposure of Nonmetallic Materials
- ASTM G155: Standard Practice for Operating Xenon Arc Light Apparatus for Exposure of Nonmetallic Materials
- SAE J2527: Accelerated Exposure of Automotive Exterior Materials Using Xenon-Arc Devices
- GB/T 16422.2: Plastics – Methods of exposure to laboratory light sources – Part 2: Xenon-arc lamps (Chinese National Standard)

Working Principle and Technical Foundation
- UV Light Simulation: The chamber employs high-intensity UV lamps that mimic the spectrum of natural sunlight, particularly the harmful UV-A and UV-B wavelengths. These wavelengths are responsible for causing photochemical degradation in plastics, leading to phenomena such as yellowing, cracking, embrittlement, and loss of mechanical properties.
- Temperature and Humidity Control: In addition to UV exposure, the chamber can precisely control temperature and humidity levels. This combination simulates various environmental conditions, from hot and humid tropical climates to cold and dry desert environments. The temperature range typically spans from -20°C to +80°C, while humidity can be controlled between 10% and 98% RH.
- Cyclic Testing: The chamber can program cyclic testing protocols, alternating between different phases of UV exposure, darkness, and varying temperature/humidity cycles. This mimics diurnal and seasonal changes, providing a more realistic simulation of outdoor exposure.
- Accelerated Aging: Based on the Arrhenius equation and acceleration factor (AF) theory, the chamber accelerates the aging process by increasing the intensity of UV light and environmental stresses. This allows researchers to predict long-term performance within a much shorter timeframe.
Technical Features
- Advanced UV Lamp Technology: Equipped with either xenon arc lamps or fluorescent UV lamps (UVA/UVB), depending on the specific application. Xenon lamps offer a broader spectrum, including visible and infrared light, while fluorescent lamps provide a more focused UV-A and UV-B output.
- Precise Environmental Control: Utilizes PID (Proportional-Integral-Derivative) controllers to maintain tight temperature and humidity uniformity, ensuring consistent test conditions across all samples.
- User-Friendly Interface: Features an intuitive touchscreen interface for easy programming of test parameters, monitoring of real-time data, and automatic logging of results. Some models also support remote access via PC or mobile devices.
- Safety and Reliability: Includes multiple safety features such as over-temperature protection, emergency stop buttons, and automatic shutdown in case of system malfunctions. Regular self-diagnostic checks ensure the chamber operates at peak performance.
- Modular Design: Offers flexible configurations to accommodate different sample sizes and shapes, making it suitable for a wide range of plastic products, from small components to large panels.

Item | Specification |
Outside dimension | 1300W×500D×1460Hmm |
Chamber material | Paint Spray |
Temperature range | RT~70℃ |
Temperature fluctuation | ±2℃ |
Temperature control | PID SSR control |
Humidity range: | ≥95%RH |
Controller | Programmable controller, LCD touch screen |
Control mode | Balance temperature humidity control (BTHC) |
Test cycle setting | Exposure, condensation and water spray test cycle is programmable |
Lamp power | 40W/Piece |
Distance from sample to lamp | 50±2mm |
Centre distance between the lamp | 70mm |
Irradiance | 0.45~0.8W/m2 (optional) |
UV lamps | Imported Atlas UV-A: 315-400nm (8pcs, 1600h lifetime) |
Standard Specimen Size | 75×290mm (24pcs) or 75x150mm (48pcs), max. thickness 5mm |
Testing time | 0~999H, adjustable |
Protection system | Overload short circuit protection Over temperature protection Water lacking protection Earth leakage protection Auto shut off protection |

Procurement Considerations
When selecting a UV aging test chamber for plastic materials, consider the following key factors:
- UV Lamp Type: Choose between xenon arc or fluorescent UV lamps based on the specific requirements of your tests. Xenon lamps provide a more comprehensive spectrum, while fluorescent lamps are more cost-effective for UV-A and UV-B testing.
- Temperature and Humidity Range: Ensure the chamber can meet the temperature and humidity conditions relevant to your application. For outdoor exposure simulations, a wider range is generally preferred.
- Test Chamber Size: Select a chamber size that accommodates your largest samples while optimizing space utilization. Consider future expansion needs if applicable.
- Control System: Look for a user-friendly control system with precise temperature, humidity, and UV intensity controls. Advanced models may offer additional features like remote monitoring and data analysis software.
- Brand Reputation and Support: Opt for a reputable manufacturer with a strong track record of quality and reliability. Ensure the supplier offers excellent customer service, technical support, and after-sales maintenance.
Usage and Maintenance
- Preparation of Samples: Prepare samples according to the relevant testing standard, ensuring they are representative of the material being tested. Clean and inspect samples before placing them in the chamber.
- Programming Test Parameters: Use the control system to set up the desired test conditions, including UV intensity, temperature, humidity, and cycle duration. Follow the manufacturer's guidelines for optimal setup.
- Monitoring and Data Collection: Regularly monitor the test progress and collect data for analysis. Some chambers allow for automated data logging and reporting.
- Maintenance and Calibration: Perform routine maintenance tasks such as cleaning the UV lamps, checking the cooling system, and calibrating the temperature and humidity sensors. Regular calibration ensures accurate and reliable test results.
- Safety Precautions: Always follow safety protocols, including wearing appropriate protective gear when handling UV lamps and chemicals. Ensure the chamber is properly grounded and that all safety features are functioning correctly.
By utilizing a UV aging test chamber, manufacturers and researchers can gain critical insights into the long-term performance of plastic materials, enabling them to develop more durable and reliable products that stand the test of time.
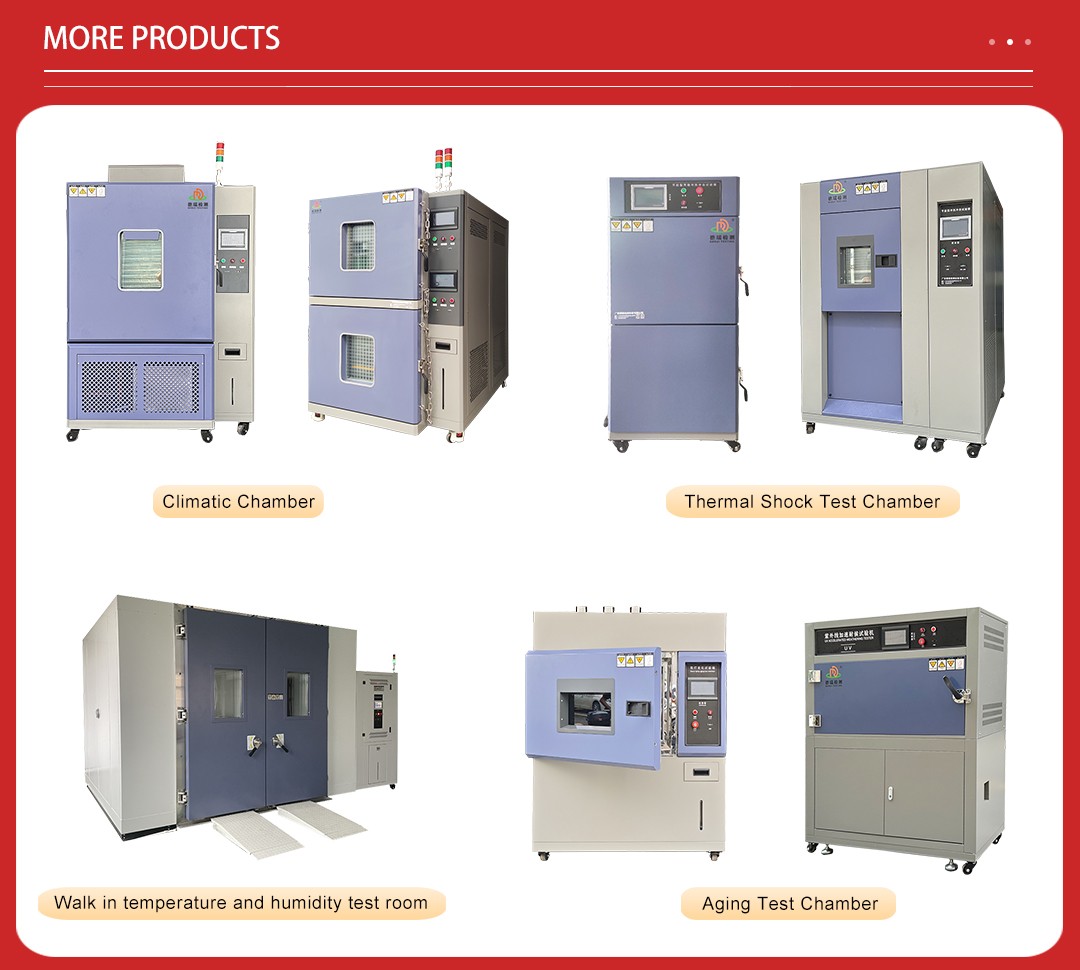
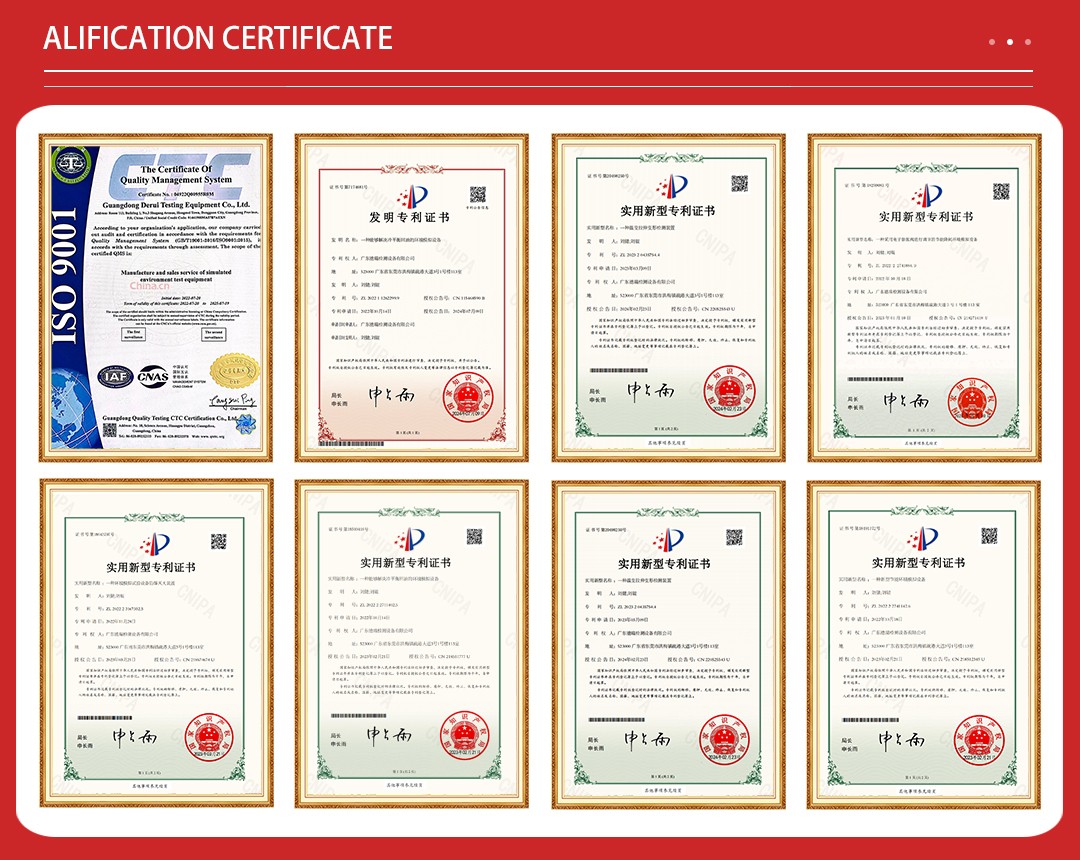